The 15-Second Trick For Alcast Company
The 15-Second Trick For Alcast Company
Blog Article
The smart Trick of Alcast Company That Nobody is Discussing
Table of ContentsThe Ultimate Guide To Alcast CompanySome Known Details About Alcast Company Indicators on Alcast Company You Should KnowThe Best Strategy To Use For Alcast CompanyThe Only Guide for Alcast CompanySee This Report on Alcast Company
The refined difference hinges on the chemical material. Chemical Contrast of Cast Aluminum Alloys Silicon promotes castability by decreasing the alloy's melting temperature and enhancing fluidness throughout casting. It plays a critical function in enabling elaborate molds to be filled properly. Additionally, silicon adds to the alloy's toughness and put on resistance, making it useful in applications where resilience is critical, such as automotive parts and engine elements.It also improves the machinability of the alloy, making it simpler to refine into completed products. In this method, iron adds to the general workability of light weight aluminum alloys.
Manganese adds to the strength of aluminum alloys and boosts workability (aluminum metal casting). It is typically utilized in functioned aluminum items like sheets, extrusions, and accounts. The visibility of manganese aids in the alloy's formability and resistance to fracturing during manufacture procedures. Magnesium is a light-weight element that provides stamina and effect resistance to light weight aluminum alloys.
The 3-Minute Rule for Alcast Company
It enables the manufacturing of lightweight components with excellent mechanical properties. Zinc boosts the castability of light weight aluminum alloys and helps manage the solidification procedure during casting. It enhances the alloy's stamina and solidity. It is commonly discovered in applications where detailed shapes and fine information are required, such as attractive castings and specific automobile components.
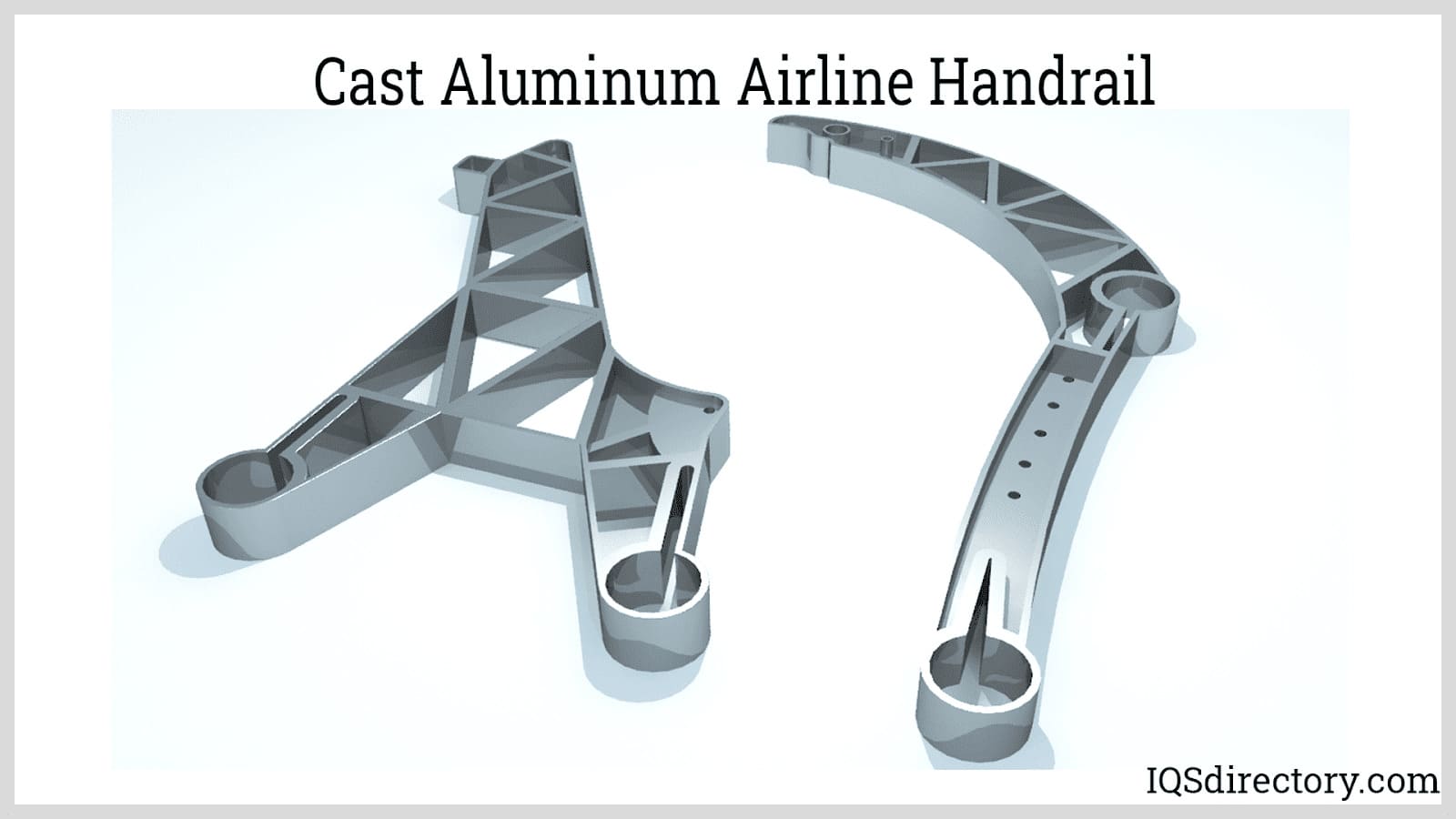
The primary thermal conductivity, tensile toughness, yield toughness, and elongation differ. Among the above alloys, A356 has the highest thermal conductivity, and A380 and ADC12 have the cheapest.
Get This Report on Alcast Company
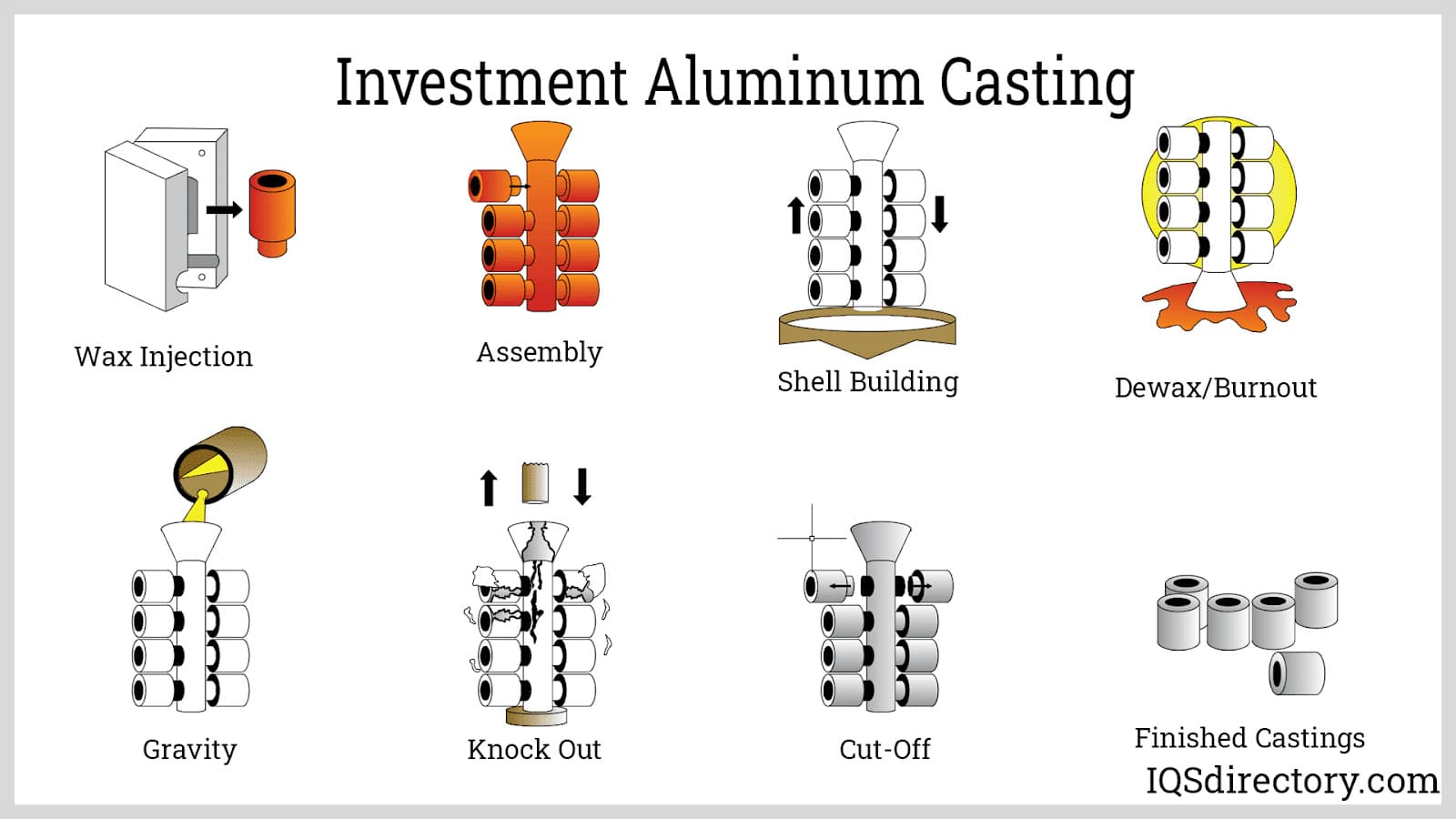
In accuracy spreading, 6063 is well-suited for applications where detailed geometries and top notch surface area coatings are critical. Examples include telecommunication enclosures, where the alloy's exceptional formability permits for sleek and visually pleasing layouts while maintaining structural honesty. Similarly, in the Illumination Solutions market, precision-cast 6063 parts create stylish and reliable lighting fixtures that require detailed shapes and excellent thermal efficiency.
It brings about a better surface area coating and better corrosion resistance in A360. Additionally, the A360 shows superior elongation, making it optimal for complicated and thin-walled parts. In precision casting applications, A360 is well-suited for industries such as Consumer Electronics, Telecommunication, and Power Devices. Its boosted fluidness enables detailed, high-precision parts like smart device cases and interaction gadget housings.
Some Ideas on Alcast Company You Should Know
Its distinct residential or commercial properties make A360 a useful choice for accuracy spreading in these markets, improving product toughness and quality. Casting Foundry. Aluminum alloy 380, or A380, is a widely used casting alloy with numerous distinct imp source features.
In accuracy spreading, light weight aluminum 413 radiates in the Consumer Electronics and Power Tools industries. It's typically utilized to craft elaborate elements like mobile phone real estates, cam bodies, and power device housings. Its precision is amazing, with tight resistances approximately 0.01 mm, ensuring flawless item setting up. This alloy's remarkable rust resistance makes it a superb selection for outdoor applications, ensuring lasting, durable products in the pointed out markets.
Alcast Company for Beginners
As soon as you have actually decided that the aluminum die casting procedure is ideal for your project, an important following action is choosing one of the most suitable alloy. The light weight aluminum alloy you select will substantially affect both the casting procedure and the homes of the final item. Due to this, you should make your choice meticulously and take an educated approach.
Determining the most ideal light weight aluminum alloy for your application will certainly mean evaluating a vast range of attributes. These comparative alloy qualities follow the North American Pass Away Spreading Organization's standards, and we've divided them into two categories. The first classification addresses alloy attributes that influence the production process. The 2nd covers qualities affecting the residential properties of the end product.
The smart Trick of Alcast Company That Nobody is Discussing
The alloy you choose for die spreading directly affects numerous aspects of the casting process, like how simple the alloy is to work with and if it is prone to casting problems. Warm cracking, also called solidification splitting, is a typical die spreading problem for light weight aluminum alloys that can result in internal or surface-level splits or cracks.
Particular aluminum alloys are extra at risk to hot cracking than others, and your selection should consider this. Another common flaw discovered in the die casting of aluminum is pass away soldering, which is when the actors adheres to the die wall surfaces and makes ejection tough. It can damage both the actors and the die, so you should search for alloys with high anti-soldering homes.
Rust resistance, which is currently a notable quality of light weight aluminum, can differ considerably from alloy to alloy and is a vital particular to think about relying on the ecological conditions your item will be subjected to (aluminum metal casting). Put on resistance is an additional residential or commercial property typically sought in aluminum products and can distinguish some alloys
Report this page